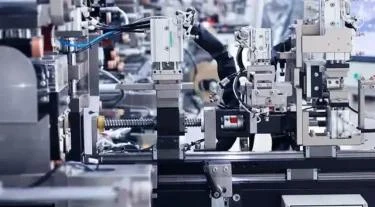
# Tape Production Process and Techniques
## Introduction to Tape Manufacturing
Tape manufacturing is a complex process that involves multiple stages to create adhesive products for various applications. From everyday household tapes to specialized industrial adhesives, the production of tape requires precision engineering and careful material selection.
## Raw Materials in Tape Production
The foundation of any tape product lies in its raw materials. Manufacturers typically use:
– Backing materials (paper, plastic films, or cloth)
– Adhesive compounds (rubber-based, acrylic, or silicone)
– Release liners (for pressure-sensitive tapes)
– Additives (to enhance performance characteristics)
## The Tape Manufacturing Process
### 1. Backing Material Preparation
The process begins with preparing the backing material. Plastic films may be extruded or cast, while paper backings undergo special treatments for strength and flexibility. Cloth backings are woven or knitted to specific densities.
### 2. Adhesive Application
There are several methods for applying adhesive to the backing:
– Solution coating: Adhesive dissolved in solvent is applied and dried
– Hot melt coating: Thermoplastic adhesive applied in molten form
– Water-based coating: Environmentally friendly adhesive application
– 100% solids coating: No solvents or water used
### 3. Drying and Curing
After application, the adhesive must be properly dried or cured:
– Solvent-based adhesives require evaporation
– Water-based systems need careful drying to prevent bubbling
– UV or electron beam curing for certain specialty adhesives
### 4. Lamination and Winding
The finished tape is laminated with release liners if needed, then wound onto cores:
– Precision tension control ensures uniform winding
– Slitting machines cut wide rolls into desired widths
– Quality checks occur throughout the winding process
## Advanced Tape Manufacturing Techniques
Modern tape production incorporates several sophisticated techniques:
### Multi-layer Coating
Some tapes require multiple adhesive layers with different properties, applied in sequence to create complex performance characteristics.
### Microstructured Surfaces
Advanced manufacturing creates microscopic patterns on tape surfaces to enhance adhesion or create special release properties.
### Nanotechnology Applications
Incorporating nanoparticles into adhesives can dramatically improve performance characteristics like thermal conductivity or electrical insulation.
## Quality Control in Tape Production
Stringent quality measures ensure consistent tape performance:
– Adhesion testing (peel, tack, and shear measurements)
– Thickness uniformity checks
– Visual inspection for defects
– Accelerated aging tests
– Environmental resistance testing
## Environmental Considerations
Modern tape manufacturing focuses on sustainability:
– Reduction of solvent use
– Water-based adhesive systems
– Recyclable materials
– Energy-efficient production processes
– Waste minimization programs
## Future Trends in Tape Manufacturing
The industry continues to evolve with:
– Smart tapes with embedded sensors
– Biodegradable adhesive formulations
– Improved performance at extreme temperatures
– Development of stronger yet removable adhesives
– Automated production with AI quality control
From simple packaging tapes to high-tech industrial solutions, tape manufacturing remains a vital and evolving industry that combines material science with precision engineering to create products we use every day.
Keyword: tape manufacturing